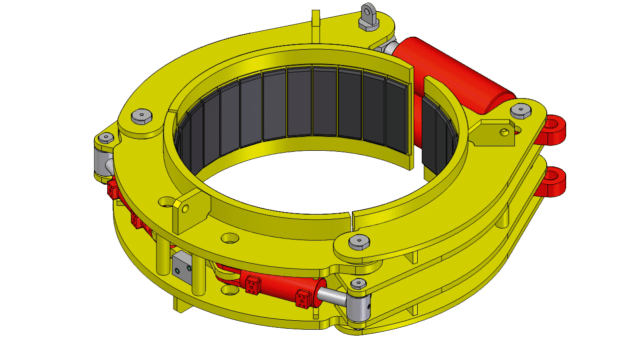
Common Issues with Pile Driver Clamps and How to Fix on Them
- by danieljack
Pile driver clamps are critical components in the pile driving process, ensuring that piles are securely held in place during installation. Their role is vital for maintaining safety, precision, and efficiency on construction sites. However, like all mechanical equipment, pile driver clamps can experience various issues that may hinder their performance and cause project delays or safety hazards.
In this article, we will explore some of the most common issues with pile driver clamps and provide practical solutions to fix them. Understanding these problems and addressing them promptly helps maintain smooth operations and extends the lifespan of your equipment.
1. Wear and Tear of Clamp Jaws
One of the most frequent issues with pile driver clamps is the wear and tear of the clamp jaws. The jaws grip the pile firmly during driving, but over time, the constant pressure and friction can cause them to degrade or lose their gripping ability.
How to Fix:
Regular inspection is key to detecting jaw wear early. If wear is significant, replace the jaws with OEM (Original Equipment Manufacturer) parts to ensure proper fit and function. Applying anti-wear coatings or using replaceable jaw inserts made from hardened steel can also extend the service life of clamp jaws.
2. Loose or Damaged Fasteners
Fasteners such as bolts and pins secure the components of pile driver clamps together. Due to constant vibration and heavy loads during pile driving, these fasteners can loosen or suffer damage.
How to Fix:
Implement a routine maintenance schedule that includes checking and tightening all fasteners. Use thread-locking compounds to prevent bolts from loosening. Replace any damaged or corroded fasteners immediately to avoid clamp failure during operation.
3. Hydraulic Leakages in Hydraulic Clamps
Many modern pile driver clamps are hydraulically operated to provide strong, adjustable gripping force. However, hydraulic systems can develop leaks, reducing clamp effectiveness and causing environmental hazards.
How to Fix:
Inspect hydraulic hoses, seals, and connections regularly for signs of wear or leaks. Replace faulty seals and damaged hoses promptly. Maintain hydraulic fluid levels and ensure the use of clean, compatible hydraulic oil. Routine hydraulic system servicing is essential to prevent unexpected failures.
4. Misalignment of Clamps
Misalignment occurs when the clamp does not position itself correctly around the pile, potentially leading to uneven gripping or slippage. This issue can be caused by structural damage, improper installation, or wear in the clamp mechanism.
How to Fix:
Realign the clamps according to manufacturer specifications during regular maintenance checks. Inspect structural components for bends or cracks and repair or replace damaged parts. Proper training of operators in clamp installation and handling also reduces the risk of misalignment.
5. Corrosion and Rusting
Pile driver clamps are often exposed to harsh environmental conditions, including moisture, saltwater (in marine projects), and dirt. These conditions can cause corrosion and rusting, weakening the clamp structure and reducing reliability.
How to Fix:
Apply corrosion-resistant coatings or paints to the clamps, especially if used in marine or humid environments. Store clamps in dry conditions when not in use. Regular cleaning and application of rust inhibitors help maintain the clamps’ integrity.
6. Inconsistent Clamping Force
If the pile driver clamps do not apply consistent force, the pile may shift during driving, leading to inaccurate placement or damage to the pile or equipment. This inconsistency can be due to hydraulic issues, mechanical wear, or improper settings.
How to Fix:
Calibrate hydraulic systems regularly to ensure consistent pressure output. Replace worn components that affect clamping pressure, such as pistons or seals. Train operators to monitor clamping force during operation and adjust settings as needed.
7. Excessive Vibration Impact
While pile driving inherently involves high-impact vibrations, excessive vibration can accelerate the degradation of pile driver clamps. Vibrations can loosen components, cause fatigue cracks, and lead to mechanical failures.
How to Fix:
Use vibration dampening accessories if available. Schedule frequent inspections to detect early signs of fatigue or cracks. Replace components showing signs of stress before failure occurs.
Best Practices for Maintaining Pile Driver Clamps
Beyond fixing individual problems, adopting a proactive maintenance approach can prevent many common issues with pile driver clamps. Here are some best practices:
-
Regular Inspections: Schedule daily and weekly checks to identify wear, leaks, or damage early.
-
Proper Training: Ensure operators understand correct installation, operation, and maintenance procedures.
-
Use Quality Parts: Always replace worn or damaged parts with manufacturer-approved components.
-
Lubrication: Apply lubricants as recommended to reduce friction and wear.
-
Record Keeping: Maintain logs of maintenance activities to track the health of the clamps and plan replacements.
Conclusion
Pile driver clamps are indispensable tools in foundation construction, but they are subject to various mechanical and environmental stresses that can lead to common issues. Addressing problems such as jaw wear, loose fasteners, hydraulic leaks, misalignment, corrosion, inconsistent clamping force, and vibration damage is essential to maintain safety and efficiency.