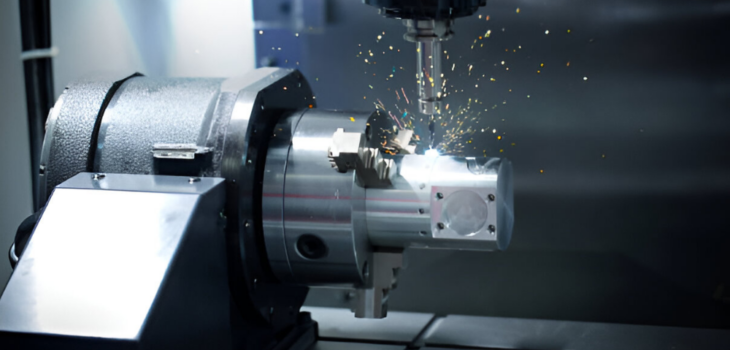
Unlocking Precision: Why CNC Milling Service Is Vital for Modern Manufacturing
Modern manufacturing demands high accuracy, repeatability, and speed—qualities that a CNC milling service delivers with precision. Whether you’re building aerospace components, automotive systems, or medical devices, CNC milling stands out as a flexible and reliable solution. If you’re seeking quality-assured, custom-machined parts, partnering with a professional CNC milling provider ensures efficiency without compromising quality.
What Is CNC Milling?
CNC milling is a subtractive manufacturing process that uses computer numerical control (CNC) technology to guide rotating cutting tools. These tools shape solid materials like metals and plastics into complex, dimensionally accurate components. Unlike CNC turning, where the material rotates, in milling, the tool moves while the workpiece remains stationary or moves along controlled axes.
How CNC Milling Service Works
A CNC milling service follows a structured process that transforms digital models into physical parts.
1. CAD Modeling
Design begins with a 3D CAD file that defines the geometry, tolerances, and features of the part.
2. CAM Programming
The CAD model is imported into CAM software to generate G-code, the instructions the CNC machine will follow.
3. Machine Setup
Operators secure the raw material onto the machine bed, load tools, and verify machine calibration.
4. Milling Process
The machine uses programmed toolpaths to remove material, shaping the workpiece to exact specifications.
5. Final Inspection
Dimensional inspections and quality control tests ensure each part meets project requirements.
Benefits of Choosing a CNC Milling Service
Partnering with an experienced CNC milling provider offers both operational and strategic advantages.
1. Unmatched Precision
Modern CNC mills operate with tolerances as tight as ±0.001 inches, making them ideal for intricate parts where accuracy is critical.
2. Scalability
Whether you need a prototype or thousands of units, CNC milling scales easily without a drop in quality.
3. Fast Turnaround
Automation and efficient programming allow for quicker part delivery compared to manual machining.
4. Cost Efficiency
Although upfront setup may seem high, CNC milling reduces labor, waste, and revision costs in the long run.
5. Material Versatility
CNC milling works on metals, plastics, composites, and even wood, making it adaptable to nearly any industry.
Common Industries That Rely on CNC Milling Services
Industry | Application Examples |
Aerospace | Turbine blades, brackets, housings |
Automotive | Gearboxes, pistons, intake manifolds |
Medical | Implants, surgical instruments, diagnostic tools |
Electronics | Enclosures, heat sinks, casings |
Industrial | Jigs, fixtures, mechanical assemblies |
These industries depend on CNC milling services for quality, consistency, and speed across varied production volumes.
Types of CNC Milling Machines
Understanding different machine types can help determine the right setup for a given part.
Vertical Milling Machines
These are the most common type, where the spindle is positioned vertically. Suitable for face milling, end milling, and drilling.
Horizontal Milling Machines
With a horizontal spindle orientation, these machines are ideal for cutting deeper grooves or slots in thicker materials.
Multi-Axis CNC Mills
- 3-Axis Machines: Good for basic milling tasks on flat surfaces.
- 4-Axis Machines: Adds rotary movement, useful for complex parts.
- 5-Axis Machines: Offers complete spatial flexibility, essential for high-precision components with intricate geometries.
Key Materials Used in CNC Milling
CNC milling accommodates a broad spectrum of materials to meet structural, functional, and aesthetic requirements.
Material | Characteristics |
Aluminum | Lightweight, corrosion-resistant, easily machinable |
Stainless Steel | Durable, rust-resistant, suitable for medical parts |
Brass | Aesthetic, easy to machine, used in electronics |
Titanium | Strong and lightweight, used in aerospace/medical |
Engineering Plastics | Lightweight, insulating, cost-effective |
Material choice affects speed, tooling, and finishing, making it crucial for pricing and design optimization.
Applications of CNC Milling Service in Real-World Projects
1. Aerospace Component Manufacturing
Tight tolerances and complex shapes are a hallmark of aerospace parts. CNC milling ensures that components such as landing gear housings or avionics mounts are structurally sound and lightweight.
2. Precision Medical Parts
From orthopedic implants to handheld surgical devices, CNC milling creates biocompatible and intricate products used in life-saving procedures.
3. Automotive Prototyping
Need a functional engine block prototype or a precision clutch plate? CNC milling allows automotive engineers to test and refine parts before mass production.
4. Consumer Electronics Enclosures
High-end CNC milling services are used to create polished, precise enclosures that protect electronics while enhancing their aesthetics.
CNC Milling vs. Other Machining Methods
How does CNC milling compare with turning, 3D printing, or laser cutting?
Feature | CNC Milling | Turning | 3D Printing |
Motion Type | Cutting tool moves, workpiece fixed | Workpiece rotates | Layer-by-layer additive process |
Ideal For | 3D shapes, flat surfaces, complex cuts | Cylindrical parts | Rapid prototypes, light-duty parts |
Precision | Very high | High | Moderate |
Material Use | Metals, plastics, composites | Metals, plastics | Limited material variety |
Scalability | Excellent for large volumes | High for simple parts | Moderate |
For high-precision, durable components, CNC milling remains the most versatile and scalable solution.
Factors That Influence CNC Milling Costs
Several variables affect the final cost of a CNC milling service.
1. Material Selection
Harder or exotic materials like titanium increase tool wear and machining time.
2. Design Complexity
Complex parts require multiple operations, custom tooling, and extended programming.
3. Tolerances and Finishes
Tighter tolerances or specialized surface treatments like anodizing or bead blasting increase time and cost.
4. Production Volume
Higher quantities reduce the per-part cost due to setup amortization.
5. Turnaround Time
Expedited production typically incurs additional fees for prioritization and overtime.
Steps to Get Started with a CNC Milling Service
1. Submit a CAD File
Start with a detailed design including tolerances, threads, and surface finish requirements.
2. Receive a Quote
After reviewing your design, the provider will deliver a detailed cost estimate and lead time.
3. Approve and Begin Production
Once approved, programming, tooling, and machining start. In-process inspections may occur for critical parts.
4. Quality Control and Shipping
After final inspection, parts are cleaned, packaged, and shipped according to your project deadlines.
What to Look for in a CNC Milling Service Provider
The success of your project depends heavily on choosing the right partner.
1. Technical Expertise
Choose a provider with proven experience across industries and materials.
2. Equipment Capabilities
Modern shops should offer 3, 4, and 5-axis machines, tool monitoring, and in-house inspection equipment.
3. Design Support
Look for a shop that can help with Design for Manufacturability (DFM), suggesting adjustments that reduce cost and improve outcomes.
4. Lead Time Reliability
Your production schedule depends on your supplier’s ability to deliver consistently and punctually.
5. Quality Assurance
A robust QA process, including in-process checks and CMM inspection, ensures dimensional accuracy.
Future Trends in CNC Milling Services
As manufacturing evolves, so does CNC technology.
- AI-Driven Toolpath Optimization: Enhances machining efficiency and tool longevity.
- Digital Twins: Allow for real-time simulation and defect prediction.
- Hybrid Manufacturing: Combines CNC with additive manufacturing for complex parts.
- Green Machining: Focus on reducing waste, energy use, and coolant consumption.
These innovations are making CNC milling even more powerful, adaptable, and sustainable.
Conclusion: CNC Milling Service Is the Backbone of Modern Manufacturing
In today’s competitive and quality-driven environment, a CNC milling service is not just a convenience—it’s a necessity. It enables rapid prototyping, efficient production, and high-performance part fabrication across countless industries.
Whether you’re manufacturing one-off components or scaling up for global supply, CNC milling offers the precision, flexibility, and dependability modern manufacturers need to stay ahead.
For businesses serious about accuracy, reliability, and growth, investing in a trusted CNC milling service is a strategic step forward.