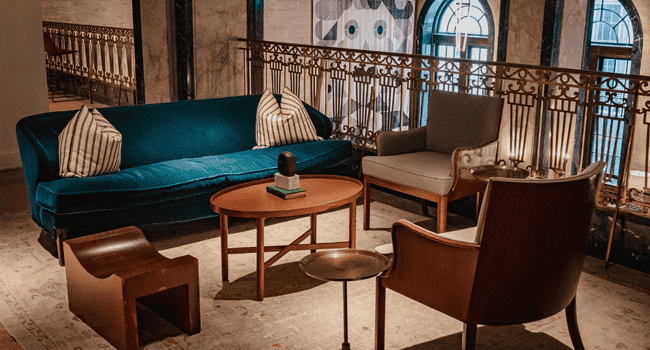
VR Walkthroughs for Clients: Visualizing Custom Millwork Before It’s Built
Imagine stepping into a room where the crown molding curves like a river, the cabinetry glows with hidden lighting, and every wood grain detail feels close enough to touch—all before a single piece of wood has been cut.
This isn’t a scene from a sci-fi movie. It’s the power of virtual reality (VR) in modern millwork drafting, transforming how designers, craftsmen, and clients collaborate on custom woodwork projects.
For centuries, millwork has been a dance between artistry and precision. But even the most detailed 2D blueprints or 3D models can leave clients guessing, “Will this built-in bookshelf feel as grand as it looks on paper?” or “Does the walnut stain clash with the flooring?” VR walkthroughs erase that guesswork, turning abstract ideas into immersive experiences.
Let’s explore how this tech is reshaping the millwork industry.
From Flat Sketches to “I’m Standing in My Dream Kitchen”
Traditional design reviews often involve flipping through pages of technical drawings or squinting at 3D renders on a screen. While helpful, these methods struggle to convey scale, texture, and spatial relationships.
A client might love a sketch of a floating staircase but not realize how it dominates the room until it’s built: a costly revelation. VR changes this. Designers can now plug millwork models into VR software, letting clients slip on a headset and “walk” through their future space.
Suddenly, they’re not just looking at a cabinet design—they’re opening its doors, testing drawer slides, and seeing how afternoon light hits the oak veneer. One architect shared how a client burst into tears during a VR session: “She finally felt the warmth of the library we’d designed. That’s something no blueprint could deliver.”
How It Works: Turning Drafts into Digital Worlds
The process starts with the millwork drafts. Using tools like AutoCAD, SketchUp, or Revit, designers create detailed 3D models of custom elements—think wainscoting, fireplace mantels, or bespoke shelving. These models are then imported into VR platforms such as Enscape, IrisVR, or even gaming engines like Unreal Engine.
Once inside the VR environment, clients navigate using handheld controllers or gaze-based controls. They can:
- Change materials on the fly (“What if we swap mahogany for maple?”)
- Test functionality (Does the pocket door clear the countertop?)
- Adjust proportions (Too tall? Shrink the island in real-time)
A millwork studio in Toronto recently used VR to help a restaurant owner visualize a 20-foot live-edge bar. “In the headset, he noticed the bar’s curve blocked the servers’ path to the kitchen,” the designer explained. “We redesigned it on the spot, avoiding a $15,000 mistake.”
Why Clients (and Designers) Love It
- No More “I’ll Know It When I See It”
VR kills vague feedback. Instead of a client saying, “Make it feel cozier,” they can point to exact elements: “Lower the ceiling beams by six inches” or “Add recessed lighting here.” This clarity speeds up approvals and cuts revision cycles.
- Spotting Hidden Flaws Early
Even seasoned drafters can miss clashes between millwork and other systems. In VR, a client might notice that a planned wall paneling obscures a thermostat or that a staircase handrail feels awkward to grip. Fixing these issues digitally costs nothing compared to post-installation changes.
- Emotional Buy-In
Custom millwork is an investment. VR lets clients experience their investment long before construction starts. One designer recalled a couple debating a bold, geometric ceiling design: “The wife was unsure until she ‘stood’ under it in VR. She said, ‘Now I get it.’ That ‘aha’ moment sealed the deal.”
The Future: Beyond Basic Walkthroughs
VR’s role in millwork is still evolving. Innovations like:
- Haptic feedback gloves that let clients “feel” virtual wood textures.
- Multi-user sessions where designers, clients, and contractors meet in the same digital space from different locations.
- AI integration that auto-generates design alternatives based on client reactions during the walkthrough.
A luxury home builder in California already uses AI-powered VR to show clients how aging affects different wood finishes. “They can fast-forward 10 years to see how walnut patinas versus cherry,” the team lead says. “It’s a game-changer for material selection.”
Getting Started with VR for Millwork
Adopting VR doesn’t require Hollywood-level budgets. Many studios start with:
- Affordable headsets like Meta Quest 3 or HTC Vive Focus 3.
- User-friendly software such as SketchUp Viewer or Gravity Sketch.
- Collaborative workflows where drafters update models in real-time during client sessions.
The key? Keep it simple. “Start with one space or one feature,” advises a millwork drafter in Chicago. “Let clients play with cabinet handles or paint colors first. Once they’re comfortable, they’ll ask to explore more.”