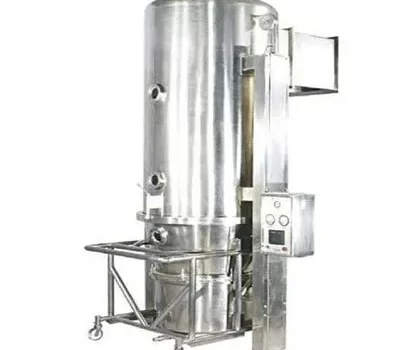
Advantages of Fluid Bed Dryer Over Traditional Drying Methods
- by montysingh
Drying is a critical process in various industries, including pharmaceuticals, food processing, and chemical manufacturing. The efficiency of a drying method significantly impacts product quality, energy consumption, and overall operational cost. Among the numerous drying techniques available, the fluid bed dryer stands out as a highly efficient and advanced technology that offers significant advantages over traditional drying methods such as tray drying, rotary drying, and spray drying. This article explores the key benefits of the fluid bed dryer and how it enhances drying efficiency in industrial applications.
1. Enhanced Drying Efficiency
One of the primary advantages of a fluid bed dryer is its superior drying efficiency compared to conventional methods. Traditional drying techniques, such as tray drying, rely on heat conduction, which can be slow and inconsistent. In contrast, the fluid bed dryer utilizes hot air to create a fluidized state, allowing for rapid and uniform heat transfer. This results in faster drying times, reducing the overall processing duration and increasing production throughput.
Unlike rotary dryers, which require continuous rotation to expose materials to heat, the fluid bed dryer ensures even exposure without mechanical movement. This eliminates the risk of material overheating or under-drying, thus improving the consistency and quality of the final product.
2. Uniform Drying and Temperature Control
Temperature control plays a crucial role in the drying process, particularly in industries where heat-sensitive materials are involved. The fluid bed dryer allows for precise temperature regulation, ensuring that materials dry uniformly without degradation. Traditional methods such as tray drying often suffer from temperature fluctuations, leading to uneven drying and potential product damage.
Moreover, the fluidized state created in a fluid bed dryer enables excellent heat and mass transfer, maintaining a consistent drying environment. This is particularly beneficial for pharmaceutical applications, where maintaining product integrity is essential.
3. Energy Efficiency and Cost Savings
Energy consumption is a significant concern in industrial drying processes. Traditional drying methods, such as spray drying, require a substantial amount of energy to evaporate moisture. In contrast, the fluid bed dryer operates at a lower temperature while achieving the same or better drying efficiency.
By using a controlled airflow system, the fluid bed dryer minimizes heat loss and optimizes energy utilization. Additionally, it reduces the need for excessive ventilation and cooling, leading to lower operational costs. Companies seeking sustainable manufacturing solutions often opt for fluid bed dryers due to their energy-saving potential.
4. Improved Product Quality
Maintaining product quality during drying is crucial, particularly in the food and pharmaceutical industries. Traditional drying methods can lead to issues such as over-drying, uneven moisture distribution, or degradation of active ingredients.
The fluid bed dryer prevents these issues by ensuring consistent drying throughout the material. The controlled environment prevents excessive thermal stress, preserving the chemical and physical properties of the product. Additionally, the gentle handling of materials reduces the risk of particle breakage, making it ideal for fragile substances.
5. Reduced Drying Time
Compared to conventional drying techniques, the fluid bed dryer significantly reduces drying time. Tray drying, for example, requires extended periods to ensure complete moisture removal, leading to bottlenecks in production. Similarly, rotary dryers, though effective, take longer to achieve uniform drying due to their mechanical nature.
In contrast, the fluid bed dryer accelerates the drying process by suspending particles in hot air, allowing for rapid moisture evaporation. This increased efficiency enables manufacturers to process larger batches within shorter timeframes, enhancing productivity and reducing downtime.
6. Versatility in Application
One of the major advantages of a fluid bed dryer is its versatility. It can be used for drying a wide range of materials, including powders, granules, and crystalline substances. Traditional drying methods may not be suitable for certain materials due to limitations in heat transfer mechanisms or the need for additional processing steps.
Fluid bed dryers can be adapted to different industries, including pharmaceuticals, chemicals, food, and agriculture. Whether drying active pharmaceutical ingredients (APIs) or food products like grains and spices, the fluid bed dryer provides optimal results without compromising quality.
7. Scalability and Customization
As industries grow, the need for scalable drying solutions becomes essential. Traditional drying methods often require extensive modifications to scale up operations, leading to increased costs and complexities.
Fluid bed dryers offer scalability by allowing customization based on production requirements. Manufacturers can choose different sizes, air distribution systems, and drying conditions to meet their specific needs. This adaptability ensures seamless integration into existing production lines without significant disruptions.
8. Reduced Maintenance and Cleaning Requirements
Another significant advantage of fluid bed dryers over traditional methods is their ease of maintenance and cleaning. Tray dryers, for instance, require frequent cleaning due to material buildup on trays, leading to higher labor costs and downtime.
Fluid bed dryers, however, feature self-cleaning mechanisms and minimal material accumulation, reducing the need for frequent maintenance. Additionally, their design allows for easy access to internal components, facilitating quicker cleaning and servicing. This is particularly beneficial in industries with strict hygiene standards, such as pharmaceuticals and food processing.
9. Environmentally Friendly Drying Process
With growing concerns about sustainability and environmental impact, industries are actively seeking eco-friendly drying solutions. Traditional drying methods often generate high emissions and waste energy through inefficient heat transfer mechanisms.
The fluid bed dryer addresses these concerns by utilizing efficient heat exchange and minimizing energy consumption. Additionally, it reduces dust generation and airborne contamination, contributing to a cleaner production environment. Manufacturers looking to adopt green practices can benefit from the reduced environmental footprint of fluid bed dryers.
10. Enhanced Process Control and Automation
Modern industrial processes demand precision and automation to enhance efficiency. Traditional drying methods often require manual intervention, increasing the likelihood of errors and inconsistencies.
Fluid bed dryers integrate advanced control systems that allow operators to monitor and adjust drying parameters in real time. Automated temperature control, airflow regulation, and moisture monitoring ensure optimal drying conditions without human intervention. This level of control enhances process reliability and minimizes product variability.
Conclusion
The advantages of fluid bed dryers over traditional drying methods are evident across multiple industries. From enhanced drying efficiency and uniform moisture removal to energy savings and improved product quality, fluid bed dryers provide a superior solution for industrial drying applications. Their versatility, scalability, and environmental benefits make them an ideal choice for manufacturers looking to optimize their drying processes.
As technology continues to evolve, the adoption of fluid bed dryers is expected to increase, further driving efficiency and sustainability in industrial drying operations. With their ability to deliver consistent, high-quality results while reducing operational costs, fluid bed dryers remain a preferred drying solution for modern manufacturing processes.